
 The Maker...
 The Knives...
Stainless or High Carbon Steel Which is best?
How I Make Cable Damascus
|
How To Make A 2" By 72" Belt Grinder
When pricing a good belt grinder I found that the features that I wanted made for a hefty price tag. First I wanted a variable speed grinder for running belts slow for fine belts. Second was that I wanted one that had a way for a small wheel for finger choils and other detail work. Here is what I came up with.
First a trip to the steel junk yard for the base and other pieces. What I choose for the base was a cut off piece of a large u channel that is about 35 pounds of weight. This was good to reduce vibration. It is 12 inches wide and about 24 inches long. Then find square bars that fit into each other. This is for the arm that will hold the belt adjuster (also called a back stand idler). It is important that these two bars slide up and down without wobble. This take some series scrounging. The tube that I found would not fit perfectly but was close enough that all I had to do was a little grinding on the edges for a good fit. About assembling this piece; Bars should be about 2 feet long. Place bars into each other and drill a series of holes starting 3 inches from bottom and make holes about 1 inch apart. Drill 5 holes that are three eights thick. This is for adjusting the arm when assembled. Drilling both at the same time for alignment. Drill a 5/8" hole at the bottom. This hole is to mount the arm to the side of the u channel plate. This mount is located at the front of the u channel on the right side. Then you'll need to locate an angle iron that is 2 inches wide on both sides. This pieces is a foot long and used for the platen which the belts ride on. Buy more than a foot because you will need pieces of this to act as mounting brackets on the arm. Two pieces are welded for the platen and to the platen. You can build your own backstand idler or you can order them from Texas Knife Makers Supply in Houston. A spring is used inside the large square bar for tension. You should find these at good hardware stores. When you put a belt on the machine this will keep the tension. This is what the adjustment holes are for. It will allow you to get the adjustment correct.
Purchase four pillow blocks for the shafts. These should be for a three quarter inch shaft. Purchase shaft and have a machine shop cut a key-way slot in the shafts. You need two shafts. One shaft is used for the contact wheel and one shaft for a step down pulley. Theses pulleys can be bought at most good hardware stores. This gives you three speeds. More hassle and money but a great addition for the belt grinder. The front shaft should be cut about 14 inches long and key-way should be centered. Have the machine shop turn down the shaft to a half inch that is two inches long. This is for grinding finger choils and will act as a contact wheel. When you assemble this take the shaft to a auto parts house and find a hose that you have to force on the turned portion of the shaft. Makes a good wheel that you can use and not worry about over heating like with some of the expensive machines on the market. Plus no hassle in having to change over from one wheel to the other. The other end of the shaft will have to be turned and threaded (with reverse threads) to accept the contact wheel. Purchase the contact wheel first to determine thread size. I know that these are not cheap but I believe Coote Belt Grinder Company has the best prices on them. Be sure to get one that is serrated. The size you chose will be determined on the grinding you want to do. For hollow grinds it is best to have at least a 8 inch wheel.For flat grinding you can use a six inch wheel. This is the size wheel that I choose. I can hollow grind with it but it took some real practice.
Find a u channel that is six inches long and 4 inches wide. This will be welded at the front of the u channel with it being six inches high, and in the middle of the large u channel that is the base. Before you weld the six by four channel it will have to be cut to allow the belt a pulley to go through it. The pillow blocks will have to be mounted on the face of the six by four inch channel. Then about 12 inches back mount the other pillow blocks. I welded two large nuts on the front side of these pillow blocks about an inch back from where they are mounted. The holes should be elongated for adjustment of belt tension. If you are using the three step down pulleys, your pillow blocks will have to be mounted high enough to have clearance from the base. You will have one step down pulley on the motor. This will mean you need two belts. One from the motor to the shaft that is in the back and one for the main shaft. I used a strong hinge to mount the motor and a spring for tension. A back stand idler will have to be used for the small side of the shaft and one for the main contact wheel.
I chose a 2 horse-power motor that is sealed for protection from dust. This is a must unless you have a supply of motors.
Last, I know that this article is not exact on all sizes of parts. You need to dry fit before welding and for those who do not weld you should be able to plan a way where just holes are drilled and threaded.
I ended up spending about $500.00 for my machine, saving quite a bit, and I love it. I have been grinding on it for about 5 years. I have had to change out a pillow block but have had no problems.
If you have a question e-mail me and I will try to help. Good luck.
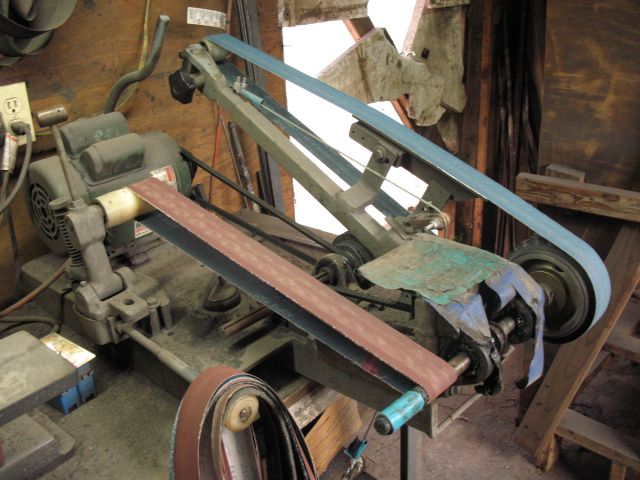 |
|